10 Warehouse KPIs for Efficient Performance
As an ecommerce business grows, it can become more challenging to keep track of the various costs and profits of your business. It’s for this reason that many tools provide a range of Warehouse KPI’s (key performance indicators) that give you insight at a glance.
Depending on your business, some KPIs will be more applicable than others however we’ll run through 10 of the most commonly used and explain how each can provide actionable information that you can build on to improve efficiency and profitability without compromising customer satisfaction. We’ll also provide a brief insight into our Warehousing product and the way that it can contribute to increased efficiency for your business.
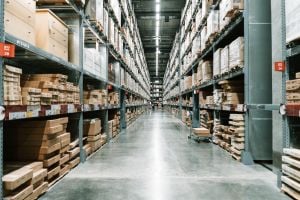
- What is a KPI in a Warehouse Context
A Key Performance Indicator (KPI) in a warehouse is a measurable value that demonstrates how effectively a warehouse is achieving key business objectives. KPIs are used to evaluate the success at reaching targets, helping warehouses to monitor efficiency, productivity, and overall performance.
- How to Measure Warehouse KPIs
Warehouse KPIs are measured by collecting data related to specific metrics that reflect the warehouse’s operational performance. This involves using warehouse management systems (WMS) to track and analyse data such as order accuracy, inventory levels, and shipping times. The measurement process includes setting benchmarks, monitoring real-time data, and comparing performance against set goals.
- What are Examples of Warehouse KPIs
The KPIs for a warehouse include Order Picking Accuracy, Inventory Turnover, Order Cycle Time, On-Time Shipping Rate, and Cost Per Order. These indicators help in assessing the efficiency of inventory management, the accuracy and speed of order fulfilment, and the overall cost-effectiveness of warehouse operations.
- 3PL Warehouse KPIs
For Third-Party Logistics (3PL) businesses, KPIs focus on metrics that evaluate the service quality and efficiency provided to their clients. These include Inventory Accuracy, Order Fulfilment Accuracy, and the Percentage of Orders Shipped on Time. 3PL warehouses also monitor Return on Investment (ROI) to assess the profitability and effectiveness of their operations.
- KPIs for Warehouse Staff
Examples of KPIs specifically relevant to warehouse staff include Labour Productivity, which measures the efficiency of the workforce by dividing total output by total labour hours, and Capacity Utilisation, which assesses how well the warehouse uses its available storage space.
- 1) Order Picking Accuracy
Order picking accuracy is a fundamental warehouse KPI measuring the percentage of orders picked without errors. It is calculated by dividing the number of accurately picked orders by the total number of orders fulfilled. This KPI directly impacts customer satisfaction and order fulfilment. High order picking accuracy ensures that customers receive the correct products in a timely manner, leading to improved customer satisfaction, reduced returns, and increased operational efficiency.
Formula: Number of accurately picked orders / Total numbers of orders fulfilled
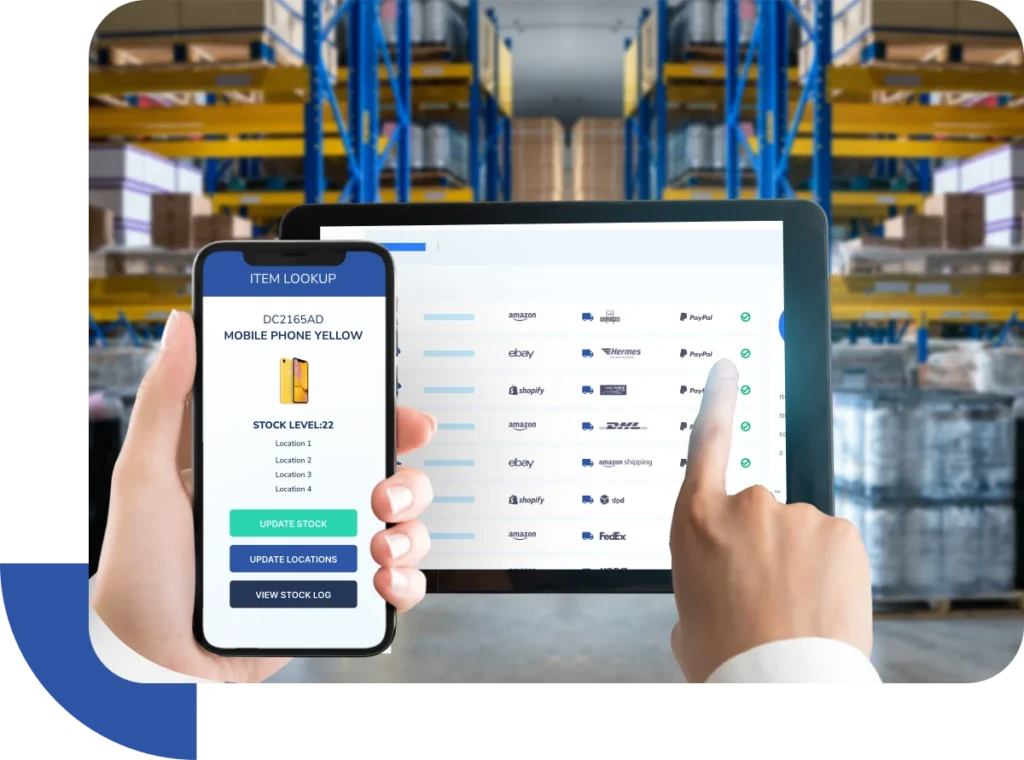
- 2) Inventory Turnover
Inventory turnover is a critical KPI that assesses the efficiency of inventory management. It measures how quickly inventory is sold and replenished within a specific period. Inventory turnover can be worked out by dividing the cost of goods sold (COGS) by the average inventory value. A higher inventory turnover ratio indicates that inventory is being efficiently utilised and that capital is not tied up in excessive stock. This KPI helps businesses optimise inventory levels, reduce carrying costs, and prevent obsolescence.
Formula: Cost of goods sold / Average Inventory
- 3) Order Cycle Time
The time it takes for an order to move through the entire order processing cycle, from order placement to delivery, is measured as the order cycle time – including order processing, picking, packing, and shipping. The calculation involves tracking the average time taken for each step and summing them up. Monitoring order cycle time is crucial for evaluating order processing speed and efficiency. By reducing cycle time, businesses can improve customer satisfaction, minimise order lead times, and enhance overall operational effectiveness.
Formula: Net Production Time / No. Units Produced
- 4) On-Time Shipping Rate
The on-time shipping rate measures the percentage of orders shipped within the promised or expected delivery time. It is calculated by dividing the number of orders shipped on time by the total number of orders. This KPI is directly linked to customer satisfaction and reputation. Maintaining a high on-time shipping rate builds trust with customers, enhances brand loyalty, and strengthens customer relationships. It also helps businesses avoid penalties associated with late shipments and improve overall operational efficiency.
Fomula: Total Orders Delivered / Deliveries That Arrived After Promised Delivery Date
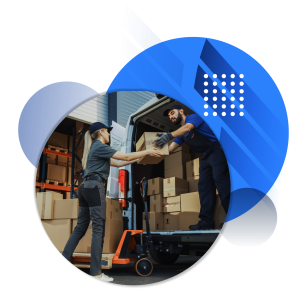
- 5) Cost Per Order
Evaluating the efficiency of warehouse operations can be done with the cost per order, achieved by calculating the average cost incurred to fulfil a single order. It includes expenses related to labour, equipment, packaging materials, shipping, and other operational costs. Monitoring the cost per order helps businesses identify areas of inefficiency and implement cost-saving measures. By optimising processes and reducing operational expenses, businesses can enhance profitability and maintain a competitive edge.
Formula: Total Warehousing Operation Costs / Number of Orders Processed
- 6) Carrying Cost of Inventory
The carrying cost of inventory assesses the expenses associated with storing and maintaining inventory over a specific period. It includes costs such as storage space, insurance, depreciation, obsolescence, and financing. Calculating the carrying cost of inventory helps businesses understand the financial impact of inventory holding and adjust inventory levels accordingly. By reducing carrying costs, businesses can improve cash flow, minimise inventory-related risks, and enhance overall warehouse profitability.
Formula: (Inventory Holding Cost / Total Value Of Inventory) x 100
- 7) Labour Productivity
Labour productivity measures the efficiency of workforce management in the warehouse by dividing the total output by the total labour hours. Monitoring labour productivity helps businesses identify opportunities to optimise staffing levels, streamline processes, and improve overall productivity. By analysing labour productivity KPIs, businesses can identify bottlenecks, implement training programs, and allocate resources effectively to maximise workforce efficiency.
Formula: Total Output / Total Labour Hours
- 8) Capacity Utilisation
To keep track of the extent to which a warehouse’s available storage capacity is being utilised, a KPI called capacity utilisation comes into play. It is calculated by dividing the actual inventory volume by the maximum storage capacity and multiplying it by 100. Monitoring capacity utilisation helps businesses optimise warehouse space and storage allocation. By maintaining an optimal level of capacity utilisation, businesses can minimise storage costs, maximise operational efficiency, and avoid stockouts or overcrowding.
Formula: (Actual Output / Maximum Possible Output) x 100
- 9) Equipment Utilisation
Equipment utilisation measures the efficiency and effectiveness of warehouse equipment. It involves tracking the usage of equipment such as forklifts, conveyors, and automated systems. Equipment utilisation is calculated by dividing the total operational hours of the equipment by the total available hours and multiplying it by 100. By monitoring equipment utilisation, businesses can identify underutilised or over utilised equipment, plan maintenance schedules effectively, and ensure smooth operations while minimising downtime and repair costs.
Formula: Total Hours of Usage / Total Number of Available Hours
- 10) Return on Investment
Return on Investment is one of the most used KPI’s so this shouldn’t be new to your business, however it would be remiss to overlook this! A comprehensive KPI, ROI assesses the profitability and effectiveness of warehouse operations and investments. It measures the financial return generated from the capital invested in the warehouse. ROI is calculated by dividing the net profit from warehouse operations by the total investment cost and multiplying it by 100. Monitoring ROI helps businesses evaluate the success of their investments, identify areas for improvement, and make informed decisions regarding future investments or expansion plans.
Formula: Net Return / Cost of Investment
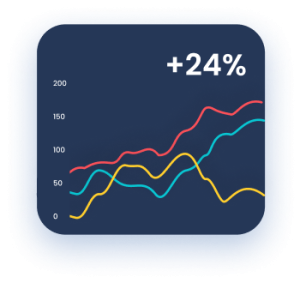
Implementing and monitoring key warehouse KPIs is essential for driving efficient operations and improving overall performance. Yet, it’s important to note that the selection of KPIs may vary depending on the unique needs and priorities of each business. By identifying and tracking the most relevant KPIs, businesses can gain a comprehensive understanding of their warehouse performance, identify areas for improvement, and make data-driven decisions to enhance operational efficiency, customer satisfaction, and profitability. With continuous monitoring and reviewing, businesses can drive continuous improvement, stay ahead of the competition, and achieve long-term success in the dynamic world of warehousing. From the above warehouse KPI examples, you should get a firm grasp of how well your warehouse operation is running. For more help, check our warehousing solution to learn how we help you stay on top of your warehouse KPIs and take your operation to new heights.